What is the cost of good quality for medical devices?
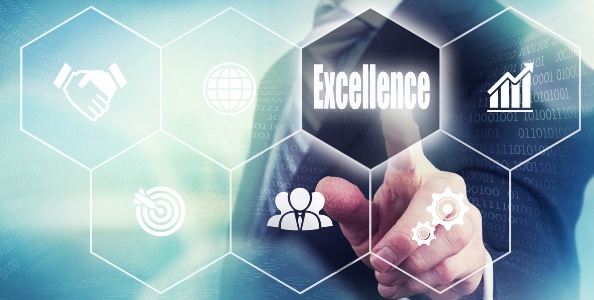
Report investigates quality-related costs in the medical devices industry
In 2011, McKinsey & Co. published a study titled Quest for Excellence - Driving a Step Change in Medical Products Operations. It investigated quality-related costs across the medical device industry. These included day-to-day quality costs as well as costs and revenue losses from non-routine, poor quality events. A second study has been completed recently to update the analysis to identify the total cost of quality for medical devices. It focused on quality operations associated with manufacturing and did not assess quality costs in research and development or commercial activities. The study also investigated the emerging best practices in which medical device companies are investing resources.
The McKinsey study looked at costs in three main categories:
- Direct costs of ensuring quality from assessing and preventing quality issues by quality and operations personnel. These include quality system support, validation, quality control, testing and inspection, auditing, and other quality activities.
- Direct costs of poor quality from
- internal and external failures including handling rejects and rework and managing deviations. These include costs related to production quality failures, such as destroyed materials, inventory changes, and fees for compliance and engineering consulting;
- remediation including investigations, corrective actions, complaint investigation, submitting reports to regulatory authorities and field actions;
- routine external quality failures including warranty costs and the cost of returned and destroyed products. Warranty costs apply especially for small electromechanical devices and capital equipment. The costs of returns and destruction can apply particularly to single-use devices.
- Indirect quality costs from loss of revenue and impact on share price due to significant quality and compliance events. These include field actions, significant observations in regulatory inspections, regulatory actions, import restrictions and consumer litigation.
The study concludes that the direct cost of quality is 6.8%-9.4% of industry sales. Worldwide sales of medical devices in 2017 were reported in the study as US $380 billion. Therefore the direct cost of quality represents US $26-$36 billion. One-third of these costs come from the direct costs of ensuring good quality; the remaining two-thirds from the direct costs resulting from poor quality. Indirect quality costs from non-routine compliance issues can increase the range by 1.5% (representing US $5.6 billion) annually.
The data presented suggest that there are significant savings available in reducing the direct costs of poor quality. The study identified five factors that correlate with good quality:
- Product and process design – implementing good practice in designing devices that are straightforward to manufacture consistently;
- People – focusing on employee retention and shared quality targets;
- Production assets – performing maintenance and renewal of manufacturing processes and equipment;
- Quality system – conducting supplier quality activities and fast but thorough investigations;
- Quality culture - involving operations personnel in quality activities.
These factors link with the US FDA ‘Case for Quality’ initiative which presents potential cost benefits to medical device manufacturers by focusing on quality during medical device design and production. This approach is indicated as paying dividends in customer satisfaction and providing significant competitive advantages. However, focusing on attaining the financial benchmarks in quality costs from the McKinsey studies without the requisite investment in achieving benchmark levels of quality performance are likely to increase direct costs of poor quality and indirect quality costs.
Author: Eamonn Hoxey, of E V Hoxey Ltd, UK, is a writer, trainer and consultant on a range of life science areas including regulatory compliance, quality management, sterility assurance and standards development
Request more information today for a call back from a member of our sales team so that you can get a better understanding of how Compliance Navigator can meet your needs.
The Compliance Navigator blog is issued for information only. It does not constitute an official or agreed position of BSI Standards Ltd or of the BSI Notified Body. The views expressed are entirely those of the authors.