The Medical Device Single Audit Program (MDSAP) audit approach document updated
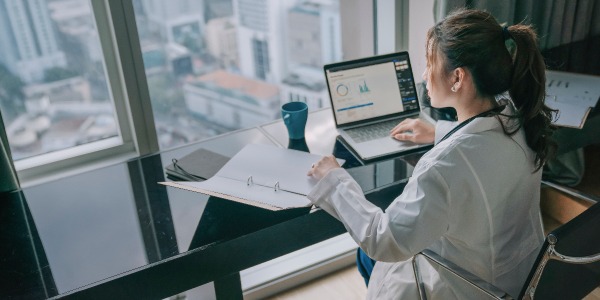
Changes introduced in the instructions for MDSAP audits
The Medical Device Single Audit Program (MDSAP) was developed to conduct regulatory audits of quality management systems (QMS) of manufacturers of medical devices. The MDSAP allows a single audit conducted by a recognized Auditing Organization (AO) to cover the requirements of BS EN ISO 13485:2016, together with specific regulatory requirements for the participating jurisdictions – Australia, Canada, Japan, Brazil and USA. Participation in the programme should reduce the need for duplicate audits and reduce the resource requirements on Regulatory Authorities and medical device manufacturers. Audits conducted in the MDSAP follow a prescribed process of defined tasks that the auditors have to perform. The audit tasks that have to be covered and the links to the applicable regulatory requirements for participating jurisdictions are identified in the MDSAP Audit Approach (MDSAP AU P0002). The 2023 update, issued in March, takes the document to revision 008.
The changes incorporated into the document are all listed in a summary of changes from the prior revision.
Perhaps the most significant change that has been made is the option to modify the sequence in which processes are audited. The MDSAP audit approach organizes the audit into a series of tasks using four primary processes and three supporting processes, in a set sequence. The revision to the Audit Approach has provided an option to audit the Production and Service Controls process after completion of the Measurement, Analysis and Improvement and followed by the Design and Development processes. This is described as a reasonable deviation from the MDSAP audit sequence.
The other changes focus on specific requirements for Canada and Australia.
For Canada:
- Clarified in the Management Process that Auditing Organizations should also consider private-labelled medical devices when verifying that products that have received marketing authorization are imported or sold in Canada;
- Added a Canadian regulatory reference in the Measurement, Analysis, and Improvement Process in the task related to assessment of design change resulting from corrective or preventive action;
- Removed hyperlinks to Canadian guidance documents in the first task for the Medical Device Adverse Events and Advisory Notices Reporting Process.
For Australia:
- Corrected a hyperlink to webpage for recalls for the second task for the Medical Device Adverse Events and Advisory Notices Reporting Processes;
- Removed the specific requirement in the Design and Development Processes related to standards used to demonstrate compliance with the Australian Essential Principles as these are not mandatory;
- Removed a reference to the International Safe Transit Association testing elements (ISTA 2A) for Australian climate zone (extreme temperature range -29C-50C) in the task related to preservation of product under the Production and Service Controls Processes;
- Removed a reference to an Essential Principles Checklist in Annex 1 Audit of Product/Process related Technologies and Technical Documentation.
Organizations participating in MDSAP should take note of the changes and consider if these will affect their preparation for initial or surveillance audits under MDSAP. MDSAP documents are also publicly available. Additional MDSAP supporting material is available on the BSI website. Helpful resources are also available on BSI’s Compliance Navigator.
The Compliance Navigator blog is issued for information only. It does not constitute an official or agreed position of BSI Standards Ltd or of the BSI Notified Body. The views expressed are entirely those of the authors.