Six steps to implement a revised standard successfully
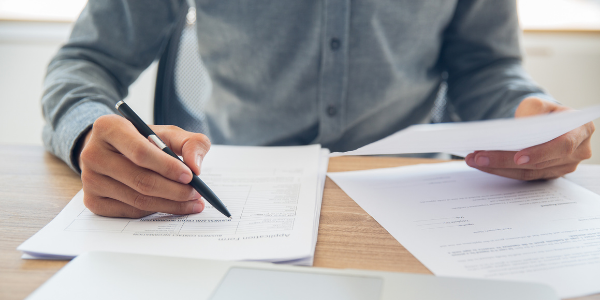
Keeping up to date with developments in standards for medical devices
The manufacturer has responsibility for the legal compliance of products intended to be placed on the market. Within this responsibility, the manufacturer has the choice of whether or not to use a particular standard. The manufacturer also needs to be able to demonstrate how they have “taken into account” the state of the art. Given that there have been a number of statements that the most recent published editions of standards should be considered as reflecting state-of-the-art, this suggests that manufacturers should give consideration to the latest version of a relevant standard, even if it is not harmonized.
Published standards have established processes to make sure that they remain current. Revisions can be triggered by identification of a specific need, such as a change in technology, the state of the art, user needs and expectations, or regulatory requirements. Standards are also reviewed on a set frequency - generally the default is a five year interval of systematic review. The outcome of the systematic review can be that the standard is confirmed without change, identified for revision, or withdrawn.
Manufacturers of medical devices should monitor developments in the standards that are relevant to them. They can do this by:
- Participating in the development of a standard in the relevant Technical Committee, Subcommittee, Working Group or Task Group at International, European or national level
- Monitoring the revision of a standard from reports provided to BSI committees doing the work or shadowing the work at International or European level
- Checking the work programmes of relevant Technical Committees made available through industry and professional associations, publicly available websites or information services.
Once the process to change a relevant standard is initiated, it is useful for manufacturers to follow the change through the various stages of development. This allows the implications of the change to be identified at an early stage and planning to implement the change to begin. Such intelligence gathering also allows input to be provided on the proposed change as it goes through the development process.
For organizations that use standards in their activities, deciding when to start the process to implement a change can depend on a variety of factors. These factors can be considered during a Gap analysis - the first step of the six step process described below.
Step 1: Carry out a gap analysis
The gap analysis considers the importance of the standard to the organization, the magnitude of the change, the effect of the change on existing devices, including devices in the supply chain and the interchangeability of spare parts, and the impact on devices at different stages of development. This analysis will inform the decisions needed in all subsequent steps of the implementation process.
Step 2: Develop an action plan with timelines, responsibilities and costs
Based on the gap analysis and the significance of the change, an action plan can be developed. This should address what needs to be done, by whom and by when. This will inform priorities as well as allow the required resources to be estimated.
Step 3: Inform senior management
Senior management will need to be informed on any implications of the change on business strategies, market access, and product approval or registration. In addition, senior management engagement will facilitate the implementation of the action plan. The information developed in the steps 1 and 2 above can give key points to brief senior leaders and gain their support.
Step 4: Update operating procedures
The gap analysis will identify what changes need to be made. These could be changes to the manufacturer’s quality management system (QMS), risk management process, device specifications, labels or instructions for use, or test methods. These changes are likely to be in procedures or documents that are controlled in the manufacturer’s QMS. Such changes need to be introduced in accordance with formal change control procedures.
Step 5: Review your training needs
The individuals who need to perform any new or revised procedures can require training in order to execute the procedures effectively.
Step 6: Update any technical documentation
The change triggered by a change to a standard can also need to be captured in the technical documentation for the device. In some instances, notified body review of changes to this technical documentation will need to be addressed.
Effective outreach and intelligence gathering about potential changes can provide a competitive advantage to an organization. Successful implementation of any change requires careful planning. Planning can begin as soon as the potential change is identified. The extent of the planning will depend on the size of the change and its importance to the manufacturer’s activities.
Author: Eamonn Hoxey, of E V Hoxey Ltd, UK, is a writer, trainer and consultant on a range of life science areas including regulatory compliance, quality management, sterility assurance and standards development
The Compliance Navigator blog is issued for information only. It does not constitute an official or agreed position of BSI Standards Ltd or of the BSI Notified Body. The views expressed are entirely those of the authors.